Exploring the World of Steel Stamping: From Layout to Manufacturing
Within the realm of manufacturing, metal stamping sticks out as a specific and effective approach for forming steel sheets right into numerous forms with remarkable consistency. From the initial style phase where elaborate patterns form to the complex manufacturing procedures, steel marking is a mix of creativity and design. Looking into this world reveals a complicated interplay of imagination and technical mastery, providing a peek into a realm where innovation meets workmanship.
Background of Steel Stamping
Steel stamping, a widely used manufacturing procedure today, has an abundant background that dates back to ancient times (Metal Stamping). The origins of steel stamping can be mapped to ancient people such as the Egyptians, that used stamping methods to adorn jewelry and ornaments with detailed layouts. Gradually, metal stamping advanced, with human beings like the Greeks and Romans using it for creating coins and decorative things

In the 20th century, steel stamping remained to develop with the assimilation of automation and computer system numerical control (CNC) modern technology. These developments better boosted the efficiency and accuracy of metal marking procedures, making it a crucial part of modern-day manufacturing throughout industries such as vehicle, aerospace, and electronics. Today, metal marking remains an essential manufacturing procedure, incorporating tradition with technology to meet the needs of a constantly developing sector.
Design Considerations and Prototyping
Style factors to consider in steel marking consist of product choice, component geometry, tooling style, and manufacturing usefulness. Tooling layout plays a substantial duty in the success of steel marking tasks, impacting component accuracy, tool durability, and production efficiency.
Prototyping is an important phase in the steel stamping process that enables engineers to examine the style, validate manufacturability, and make essential modifications prior to full-blown production. By very carefully considering layout elements and making use of prototyping, makers can streamline the steel stamping process and attain top notch, affordable manufacturing outcomes.
Tooling and Devices Essentials
Thinking about the crucial duty that tooling design plays in the success of metal marking projects, comprehending the essential tools and devices called for is paramount for accomplishing reliable production results. Tooling is a basic aspect of steel marking, as it directly affects the top quality and uniformity of the final products. Crucial tools include passes away, strikes, and components, which are custom-designed to shape and develop the steel right into the desired parts. Passes away are the key tool used to cut and develop the steel, while strikes help create holes or certain forms. Components hold the steel in position during the stamping process, making sure precision and repeatability. In addition, equipment such as stamping presses, feeders, and coil handling systems are essential for automating the stamping process and boosting efficiency. Buying high-grade tooling and equipment not only improves production efficiency but also results in higher precision, reduced waste, and overall cost savings in metal marking procedures.
Manufacturing Refine and Quality Assurance
Effectively handling the manufacturing process and executing robust top quality control procedures are vital for ensuring the success of steel stamping projects. The manufacturing process in metal marking includes a series of actions that should be carefully worked with to achieve optimum results. It starts with the preparation of resources, complied with by the setup of the marking equipment and tooling. Operators after that feed the materials right into journalism, where the stamping procedure takes location. Throughout this procedure, it is important to monitor the manufacturing line for any problems that may impact the quality of the stamped parts.
Quality assurance in metal stamping is vital to supply items check that meet the required specifications. Examining the stamped parts at different phases of manufacturing aids recognize any defects at an early stage, avoiding expensive rework or scrap. Strategies such as dimensional inspection, visual evaluation, and material testing are frequently utilized to make certain the quality of the stamped parts. By preserving strict quality assurance standards, manufacturers can copyright their credibility for delivering premium metal stamped items.
Applications and Sector Insights
In the world of steel marking, the effective application of manufacturing processes and quality control steps directly influences the effectiveness and dependability of different market other applications and supplies beneficial understandings right into the field's functional characteristics. In addition, steel marking promotes the manufacturing of numerous house devices, consisting of fridges, washing devices, and ovens, by offering affordable services for manufacturing durable and complex components. Recognizing the applications and sector understandings of metal stamping is essential for maximizing manufacturing procedures and improving product quality throughout different industries.
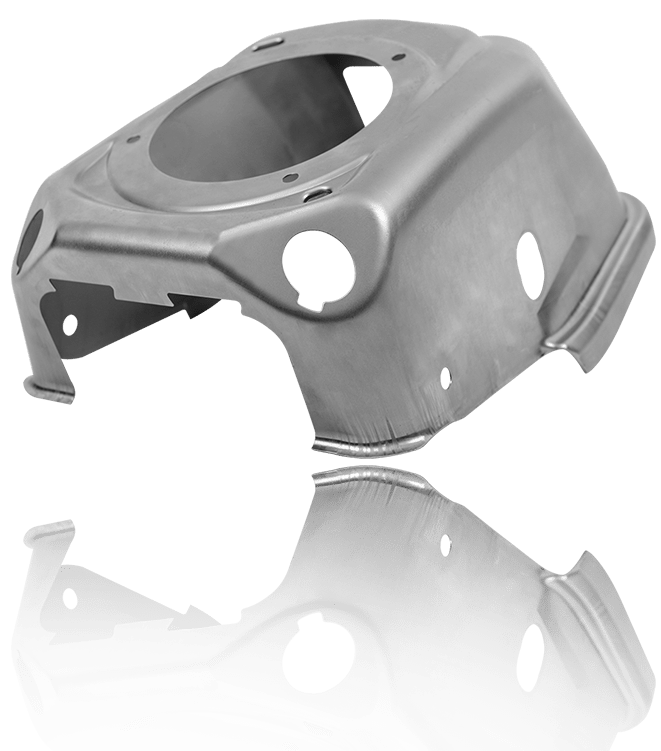
Final Thought
Layout considerations, prototyping, tooling, tools, production procedures, and quality control are essential elements Click This Link of steel stamping. With its prevalent applications and market understandings, metal marking continues to be a flexible and efficient manufacturing procedure.